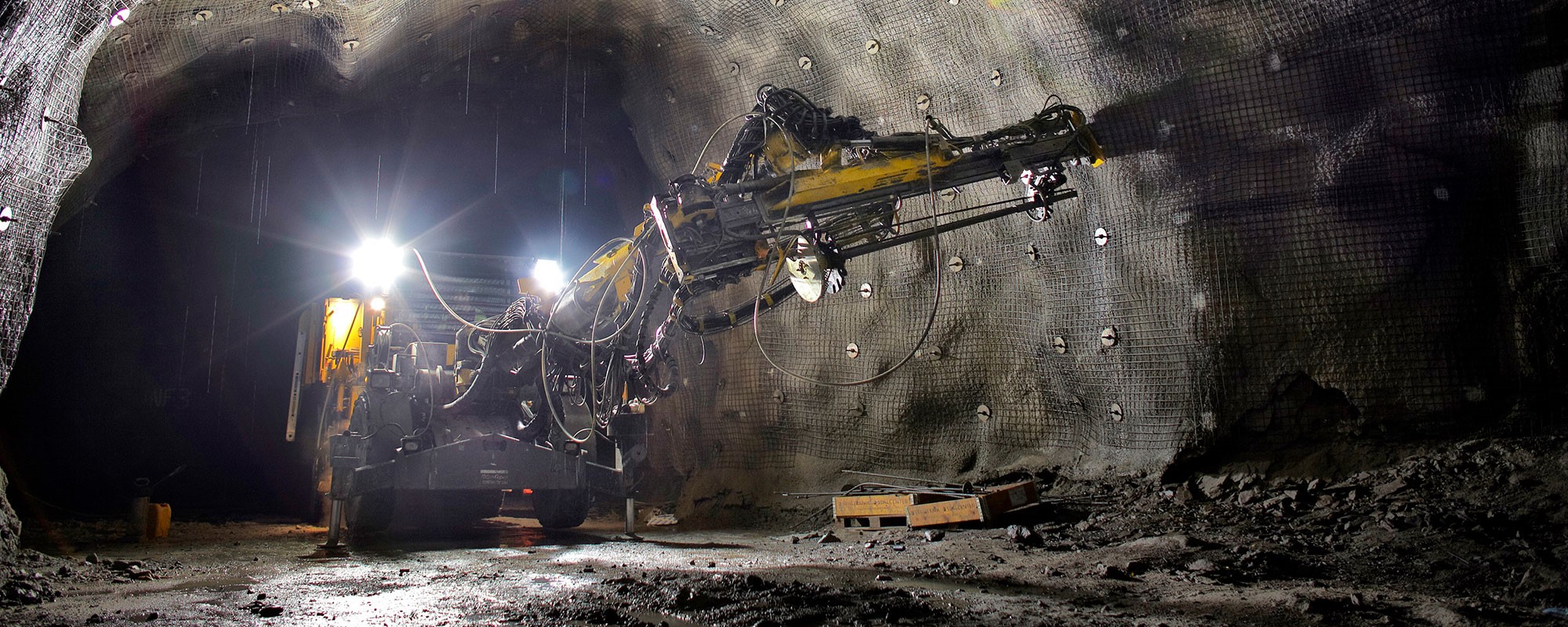
Published
- Sustainability
- Financing
Setting a new standard for sustainable mining
Leveraging digital technologies, a team of Swedish suppliers have united in developing a new standard for sustainable underground mining, capable of turning an entire industry into a carbon-free, safe workplace where robots do the dirty work.
Mining is one of the world’s oldest human endeavors and raw materials extracted from the Earth crust is what built civilizations and named historical eras, from the bronze and iron ages. Today, it is an industry often seen as having a negative environmental impact and as a dangerous place to work.
That aside, it is not an industry that we can do without. Fortunately, the advent of digital technologies and scientific breakthroughs offers wholly new ways of conducting sustainable mining. To prove this and develop a template with open standards that can be implemented at mining sites across the world, a team of Swedish suppliers along the entire value chain have joined forces in a project named Sustainable Underground Mining (SUM).
Recycling alone will not meet the growth in demand
Strong industrial heritage, long experience in advanced research of communications technology and industry cooperation is paving the way for the next export success out of Sweden. “We see a lot of interest in Swedish know-how to build sustainable underground mines around the world,” says Lotta Danielsson, Head of Automotive, Mining and Construction at EKN.
One of the participants in SUM is LKAB, Europe’s largest iron ore supplier, where Markus Petäjäniemi, Senior Vice President Market & Technology, explains the growing demand for mines:
“Steel is essential to the world and as the population increases, we need even more steel and other raw materials such as rare earth minerals, to build houses as well as smartphones. The trick is to make mining sustainable by implementing a circular thinking in every step of the value chain, from extraction to finished product and eventual recycling.”
Even as steel is the single most recycled material on the planet, recycling alone is not going to meet the growth in demand.
“Even if we increase the use of scrap metal, we cannot meet more than half the world demand for iron with scrap metal 20-30 years from now. The rest has to be made from virgin ore.”
Test mine in the far north
LKAB has joined forces with equipment producer Epiroc, vehicle manufacturer Volvo, automation system provider ABB and technical consulting firm Combitech, in building a virtual and physical test mine in Kiruna in the North of Sweden.
“What we aim to do here is develop a new standard for how to operate a sustainable mine by integrating infrastructure and people, maintenance, positioning and connectivity. How can people work together with autonomous machines and make decisions independently using input from connected digital tools? The test mine lets us simulate, validate and demonstrate new technology to reduce CO2 emissions and enable autonomous mining at greater depths without jeopardizing worker safety.”
Going deeper underground for extraction will become more important in the future, given our ever-growing appetite for more resources, and to reduce the use of strip mining that ravages the landscape and prevents land from being used for other purposes.
To facilitate the spread of the concept and create a vendor-neutral industry standard, SUM is based on an open-source thinking. “Machines and software are fully compatible and able to communicate irrespective of manufacturer, since we don’t want to lock in potential adopters.”
And SUM promises benefits in not just environmental issues, but social and economic aspects too, including increased efficiency in prospecting and extraction, says Petäjäniemi:
“Mining companies certainly benefit financially from digitally enhanced predictive analysis, more efficient extraction and the 24/7 capabilities of autonomous, automated machines.”
Consequently, SUM is a blueprint for new investments in what used to be a slow-moving, traditional industry. And, even if the concept is based on open sourcing, the Swedish companies behind it has a certain advantage on the world market: “The establishment of a common standard that has been tested and verified under real conditions offers a lot of leverage on the world market to the partners of our alliance, who benefit from a first-mover advantage in creating a solution that offers a workable way forward for the industry.”
Further along the value chain, the end users of mined materials (such as manufacturing companies) are under pressure to show that their entire supply chains are sustainable, to meet with the demands from increasingly climate-savvy consumers.
“We could have issued more debt”
The shift towards sustainable mining will obviously require new investments. LKAB launched its first green bond issuance in late 2019, the offer was oversubscribed two times and the response among investors was “fantastic”, according to Petäjäniemi: “All major pension funds and banks were there, and we could have issued much more debt.”
The total bond issue amounted to SEK 2 billion with a tenor of 5,25 years, consisting of two tranches, one floating and one fixed. Both tranches are listed on Nasdaq Stockholm’s Sustainable Bond List. The purpose of the debt is to finance sustainable mining prototypes and invest in electrical locomotives to make transports CO2 free. Before launching the green bond, LKAB invited independent consultant Cicero to verify the ESG (environmental, social and governance) sustainability of the investments and the firm rated the bond as “mid-green”, the second highest rating possible.
“Sustainability is an integrated part of LKAB's business and its strategy to ensure long-term competitiveness. The green bond allows investors to be part of the transformation of an industry that is of great significance – including globally – for the sustainable development of society,” concludes Petäjäniemi.
“LKAB aims to create value by being one of the most innovative, resource-efficient and responsible mining companies in the world. Integrating sustainability into our financing and offering a green bond fits in perfectly with our strategy,” adds Jan Moström, President and CEO of LKAB.